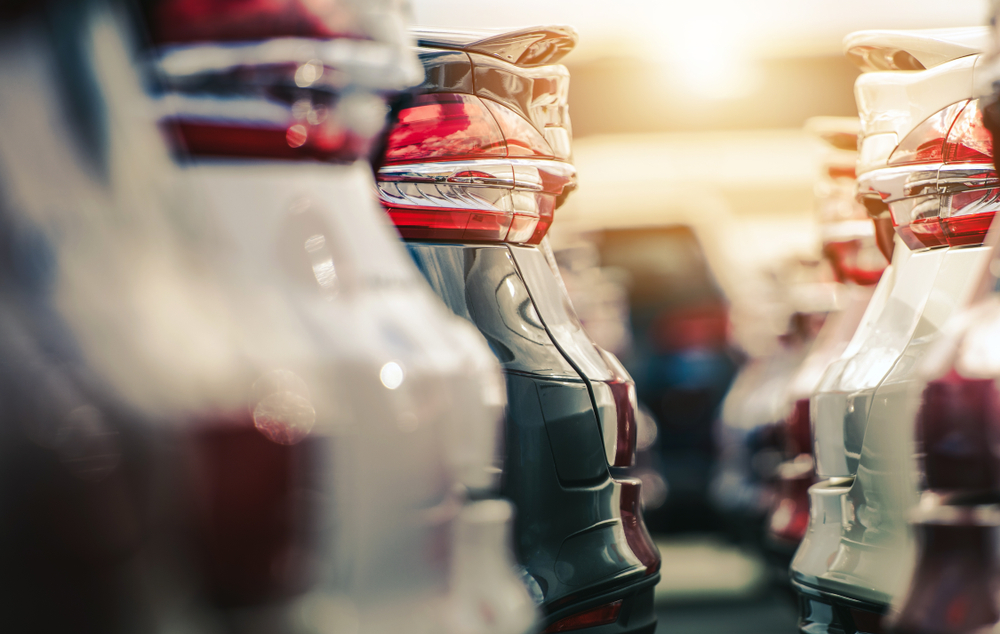
Dealing with downtime
Richard Hipkiss, managing director at Fleet Operations, explores the impact of vehicle downtime on fleets and outlines measures that fleet managers can take to minimise disruption
Fleet downtime can be a costly business, acting not only as a possible drain on a company’s finances, but on productivity levels too.
And, as recent research has revealed, productivity should be a real cause of concern for businesses.
According to the Office of National Statistics, growth in economic output per hour of work fell to a two-year low in the third quarter of 2018.
This drop highlights a need to move productivity up the priority list – particularly in a climate where economic uncertainty threatens to divert companies’ attentions.
Here, we take a further look at the impact vehicle downtime can have on businesses and offer tips on keeping a fleet running as efficiently as possible.
Don’t underestimate the cost of downtime
Underestimation of downtime is a particular issue for fleets.
Some companies will class downtime as the moment the vehicle is put in for repair but, in reality, every minute that the vehicle is off the road is downtime – and costing the company, both in financial and productivity terms.
Fleet vehicles are required to complete revenue-generating jobs and business-critical services to customers and businesses could be looking at a Vehicle Off Road (VOR) cost of between £300-£2,000 a day.
Unfortunately, it is only when significant costs have been incurred, over a long period of time, that many companies realise the true cost of downtime – and that their fleet is costing more than is being budgeted.
Most companies will not have spare vehicles in preparation for a VOR incident occurring, as this would incur further monthly costs.
With the increase of bespoke racking and specific vehicles being required for specific tasks, many jobs cannot simply be transferred to standard hire vehicles, meaning businesses have to look at work rescheduling, or very costly specialist replacement vehicles.
For larger companies with service agreements in place, cancelled jobs can incur penalties, adding more financial pressure.
It is important to point out it may be costly financially, but it can also cost businesses in terms of credibility. With social media and company reviews only a few clicks away, a missed job can turn into a customer service complaint within seconds.
Being proactive by staying on top of maintaining the specialised fleet of vehicles cannot only save businesses thousands of pounds, but in some instances, save their reputation.
Managing downtime is key
Managing vehicle downtime is crucial but companies need to be mindful of resources.
Smaller operations already have limited resources and managing vehicles, from organising services, maintenance, and fuel management, to tax, insurance and compliance, without having a dedicated fleet manager or fleet management service in place, can be extremely time-consuming.
In their absence, the task of managing fleets may fall to the business owner or MD, meaning that less time is spent on driving business growth and improving the bottom line, and more time is spent on dealing with the varied needs of their fleet.
Equally, larger companies may have stretched resources, dependent on who the remit of fleet responsibility falls to. HRs, procurement or finance directors may have an extensive fleet to look after, as well as other duties and responsibilities, so proactive vehicle management and downtime monitoring may not feature high on the priority list.
For those that don’t have a fleet manager or management service agreement in place, doing so can help protect against the redirection of vital resources. Furthermore, it can save time, due to manager’s extensive knowledge of the industry, and money – as costs, be it downtime, management or maintenance, are more easily accounted for.
That said, there are some simple measures that businesses can take that can help minimise disruption caused by downtime, if implemented and enforced effectively.
Drivers can be encouraged to carry out daily vehicle checks, which can help issues to be quickly identified and resolved. If issues are addressed in good time, simple fixes can be carried out and more serious problems avoided, which will reduce longer-term downtime.
Checks, such as looking for external damage to vehicle, oil levels, tyre condition, or diagnostic lights on the dashboard, allows drivers to spot early warning signs and report them in in a timely manner.
Carrying out regular, scheduled maintenance also means that vehicle downtime can be planned into a working day. Planning for a vehicle to be ‘on the ramp’ at a garage first thing in the morning means drivers can carry on with their daily jobs as quickly and with as little disruption as possible.
Unscheduled maintenance incidents may mean numerous jobs must be cancelled or rescheduled, affecting service levels and contractual commitments. Being proactive, and keeping on top of vehicle maintenance, will reduce the likelihood of a breakdown and ensure a smoother, more efficient operation.
Driver behaviour can directly impact a vehicle’s maintenance requirements, so driver training and management is advisable. Employee education around how drivers should drive on the roads, in order to minimise the likelihood of accidents and reduce the likelihood of unnecessary wear on the vehicle, is a worthwhile investment.
Finally, it is important for companies to remember that downtime can be minimised, but it cannot be completely eradicated. It is more a question of when downtime occurs, not if, especially if a business is running an ageing fleet.
By ensuring that vehicles are replaced at the optimum time, before they are beyond economically viable repair, maintenance and servicing costs can be significantly reduced – and productivity levels sustained.
First published on BusinessCar.